Services
Injection Molding
Injection molding produces parts by forcing molten material into a mold where it cools and hardens to the mold’s shape. JST offers cost-effective injection molding solutions, 50+ materials and 100% quality guaranteed.
What is Plastic Injection Molding?
Plastic injection molding is a process by which granular plastic is fed from a hopper into a heated chamber where it melts and hardens to create parts.
The granules are fed into the heating chamber by a screw-type plunger where they melt. As the plunger advances, the melted plastic is forced through a nozzle into the mold cavity. Since the mold remains relatively cold, the plastic solidifies almost immediately after the cavity is filled. After the plastic is injected, it must cool before the final part can be ejected from the mold.
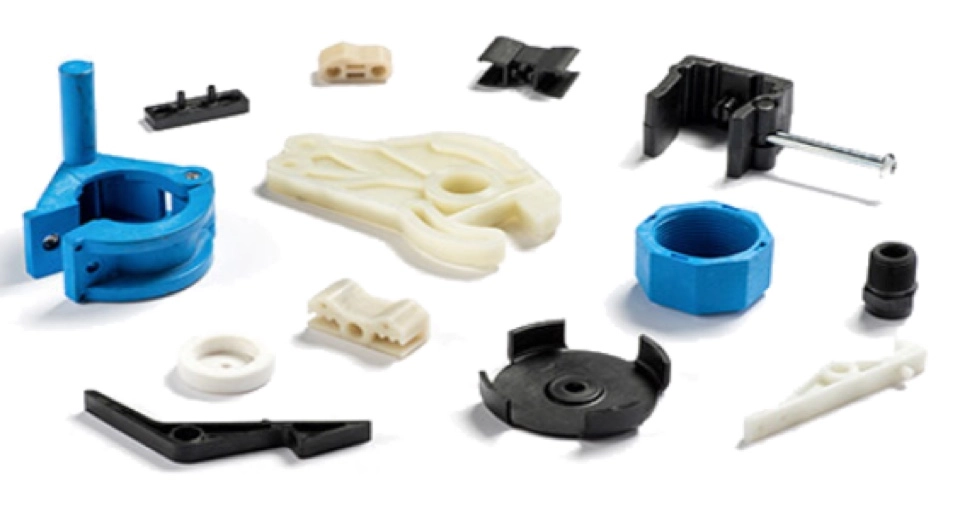
Advantages
· Economical for large quantities
· Can make almost any 2D or 3D shape
· Side and threaded holes moldable
· Finishing not required
· Insert Molding and Overmolding
Application
· Automotive
· Consumer Products
· Electronics
· Energy
· Industrial
· Medical and Dental
Compatible Materials
All thermoplastics can be injection molded. Some thermosets and liquid silicones are also compatible with the injection molding process.
ABS: Common thermoplastic with high impact resistance, low-cost and low density.
PC/ABS: Blend of two thermoplastics resulting in high impact strength, excellent thermal stability, and high stiffness.
Polyurethane (PU): Thermoplastic with high impact strength and good mechanical properties & hardness. Suitable for molding parts with thick walls.
Acrylic (PMMA): UV resistant plastic with good abrasion resistance, stiffness and hardness.
Polypropylene (PP): The most common injection molding plastic. Excellent chemical resistance. Food-safe grades available.
Polyethylene (PE): Lightweight thermoplastic with good impact strength & weather resistence. Suitable for outdoor applications.
High density polyethylene (HDPE): Excellent strength-to-weight ratio, impact and weather resistant.
Polystyrene (PS): The injection molding plastic with the lowest cost. Food-safe grades available.
Polycarbonate (PC): The plastic with the highest impact strength. High thermal resistance, weather resistance and toughness. Can be colored or transparent.
Polyvinyl Chloride (PVC): Light weight plastic with good mechanical strength and abrasion resistance. Generally used in building and construction applications.
PEEK: High-performance engineering thermoplastic with excellent strength and thermal & chemical resistance. Used to replace metal parts.
POM (Acetal/Delrin): Engineering thermoplastic with high strength, stiffness & moisture resistance and self-lubricating properties.

Additives and Fibers
JST offers additives and reinforcements as options for your plastic parts.
UV absorbers | Absorb UV radiation, slowing down the degradation of the material when used outdoors. |
Flame retardants | Prevent ignition and inhibits spread of fire. |
Plasticizers | Increase flexibility and promotes plasticity, reducing brittleness of the material. |
Colorants | Used to color plastics. |
Carbon fibers | Increase strength, toughness, and rigidity of the material at the expense of making the material more brittle. |
Glass fibers | Increase strength, toughness, and rigidity of the material at the expense of making the material more brittle. It is more flexible than carbon fibers. |
Available surface finishes for injection molding
Injection molded parts are not usually post-processed, but the mold itself can be finished to affect the surface finish of the molded part. This way aesthetic needs or technical requirements can be achieved.
Name | SPI Standard | Description |
Glossy | A-1, A-2, A-3 | The mold is smoothed and then polished with a diamond buff, resulting in parts with a mirror-like finish. |
Semi-Gloss | B-1, B-2, B-3 | The mold is smoothed with fine grit sandpaper, resulting in parts with a fine surface finish. |
Matte | C-1, C-2, C-3 | The mold is smoothed using fine stone powder, removing all machining marks. |
Textured Finish | D-1, D-2, D-3 | The mold is first smoothed with fine stone powder and then sandblasted, resulting in a textured surface. |
As Machined Finish | The mold is finished to the machinist’s discretion. Tool marks may be visible. |